Assistant Manager – Product & Process QA
Lucy Electric
Date: 10 hours ago
City: Vadodara, Gujarat
Contract type: Full time
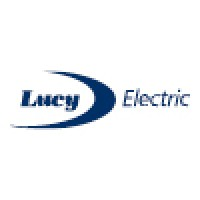
Internal Job Title: Assistant Manager – Product & Process QA
Business: Lucy Electric Manufacturing & Technologies India
Location: Halol, Vadodara, Gujarat
Job Reference No: 4099
Job Purpose
This Job Position is required for product quality assurance by establishing, implementing and maintaining the process controls and procedures with operational teams and leading continuous improvements to provide repeatable and reliable products to customers.
Job Context
This position reports directly to Manager QA.
All in-process & final inspection quality team will report to this position.
Job Dimensions & Key Accountabilities:
Be focused for all product quality concerns and provide support to manufacturing team; Determine technical aspects of product functionality, components’ criticality & assembly sequences and component properties by reviewing all aspects
Review customer complaints; implement corrective and preventive actions with root cause analysis. Elimination of major customer complaints by monitoring effectiveness of corrective and preventive actions. Analyse and formulate Risk management by implementing corrective and preventive actions to deliver reliable products to customers
Manage Product & Process Audits, Logistics, Internal Audits of ISO standards; share findings with concern departments and seek corrective and preventive actions
Active participation for controlling and reducing Cost of poor quality by identifying and monitoring the actions; Identify trends in test & inspection failures and assist with root cause analysis.
Control & reduce non-conformance trend by monitoring effectiveness of actions taken & by providing appropriate training, awareness to concern technicians. Conduct Forthrightly NCR review meeting
Participate and Serve as an active member for new product development, new processes, QCIs and product transfers by knowledge sharing and learnings.
Participate in daily production meeting, various CFT meetings to understand priorities of business and accordingly delegate tasks to team members.
Co-ordinate Engineering change(s) within team and record implementation(s), raise engineering change request as and when required for continuous improvement.
Lead process improvement activities and help identify and implement new ways of working; Prioritize and co-ordinate testing activities. Monitor trends of test results. Propose for assembly fixtures, jigs and machineries for error proofing and qualitative production output.
Prepare monthly reports as an evidence and road map of effective implementation of product quality management and the action status in line with organizational and QA objectives.
Monitor calibration plan and ensure all instruments are getting calibrated as per schedule through team support.
Establish, Improve and Retain control plans, procedures, work instructions, birth certificates and checklists for process controls
Foster an environment that supports learning, individual development, and openness to change. Provide necessary training to all concerns for continual improvement of quality. Supervise subordinates and ensure timely execution of inspection activities. Training needs assessment, recording of trainings imparted & its effectiveness review
Recommend and review the Appraisals of sub-ordinates, providing motivation to sub-ordinates to pull the maximized their efficiencies and importance in functional level, inspection, testing and assembly technique
Qualifications, Experience & Skills
Education:
Lucy Group Ltd is the parent company of all Lucy Group companies. Since its origins in Oxford, UK, over 200 years ago, the Group has grown and diversified. Today we employ in excess of 1,400 people worldwide, with operations in the UK, Saudi Arabia, UAE, India, South Africa, Brazil, Thailand, Malaysia, India and East Africa.
Lucy Electric is a global business that provides medium voltage switching and protection solutions for electrical distribution systems. Our dedication to cultivating our service provision allows Lucy Electric to offer a complete solutions package to our customers; facilitating the delivery of electricity to homes and businesses worldwide.
Does this sound interesting? We would love to hear from you. Our application process in quick and easy. Apply today!
Business: Lucy Electric Manufacturing & Technologies India
Location: Halol, Vadodara, Gujarat
Job Reference No: 4099
Job Purpose
This Job Position is required for product quality assurance by establishing, implementing and maintaining the process controls and procedures with operational teams and leading continuous improvements to provide repeatable and reliable products to customers.
Job Context
This position reports directly to Manager QA.
All in-process & final inspection quality team will report to this position.
Job Dimensions & Key Accountabilities:
Be focused for all product quality concerns and provide support to manufacturing team; Determine technical aspects of product functionality, components’ criticality & assembly sequences and component properties by reviewing all aspects
Review customer complaints; implement corrective and preventive actions with root cause analysis. Elimination of major customer complaints by monitoring effectiveness of corrective and preventive actions. Analyse and formulate Risk management by implementing corrective and preventive actions to deliver reliable products to customers
Manage Product & Process Audits, Logistics, Internal Audits of ISO standards; share findings with concern departments and seek corrective and preventive actions
Active participation for controlling and reducing Cost of poor quality by identifying and monitoring the actions; Identify trends in test & inspection failures and assist with root cause analysis.
Control & reduce non-conformance trend by monitoring effectiveness of actions taken & by providing appropriate training, awareness to concern technicians. Conduct Forthrightly NCR review meeting
Participate and Serve as an active member for new product development, new processes, QCIs and product transfers by knowledge sharing and learnings.
Participate in daily production meeting, various CFT meetings to understand priorities of business and accordingly delegate tasks to team members.
Co-ordinate Engineering change(s) within team and record implementation(s), raise engineering change request as and when required for continuous improvement.
Lead process improvement activities and help identify and implement new ways of working; Prioritize and co-ordinate testing activities. Monitor trends of test results. Propose for assembly fixtures, jigs and machineries for error proofing and qualitative production output.
Prepare monthly reports as an evidence and road map of effective implementation of product quality management and the action status in line with organizational and QA objectives.
Monitor calibration plan and ensure all instruments are getting calibrated as per schedule through team support.
Establish, Improve and Retain control plans, procedures, work instructions, birth certificates and checklists for process controls
Foster an environment that supports learning, individual development, and openness to change. Provide necessary training to all concerns for continual improvement of quality. Supervise subordinates and ensure timely execution of inspection activities. Training needs assessment, recording of trainings imparted & its effectiveness review
Recommend and review the Appraisals of sub-ordinates, providing motivation to sub-ordinates to pull the maximized their efficiencies and importance in functional level, inspection, testing and assembly technique
Qualifications, Experience & Skills
Education:
- Full time engineering graduate from an AICTE affiliated university and minimum 10+ years post qualification working experience in switchgear industry (preferrable)
- Proficient in problem solving techniques and drive to achieve continual improvements
- Knowledge of assembly techniques and various manufacturing processes
- Expert in Auditing of manufacturing processes, vendors and ISO standards requirements
- Experience in lean manufacturing, 5s and Kaizen concepts
- Hands-on experience in ISO 9001, 14001, 45001
- Knowledge of performing test of almost all switchgear products for insulation, mechanical and electrical requirements
- Excellent communication skills, Team Player
- Integrity and professional ethics
- Leads by example and inspires our people to do the right thing
- Cooperates and works across the organization to deliver the business results
- Encourages challenge to foster new ideas and ways of doing things
- Gets things done and makes it easy for others to do the same
- Builds authentic, effective working relationships
- Values our culture and actively encourages sharing different points of view
- Has a positive can-do attitude
- Openly encourages debate to achieve the best outcomes
- Open to giving and receiving feedback; identifies, coaches and develops future talent
Lucy Group Ltd is the parent company of all Lucy Group companies. Since its origins in Oxford, UK, over 200 years ago, the Group has grown and diversified. Today we employ in excess of 1,400 people worldwide, with operations in the UK, Saudi Arabia, UAE, India, South Africa, Brazil, Thailand, Malaysia, India and East Africa.
Lucy Electric is a global business that provides medium voltage switching and protection solutions for electrical distribution systems. Our dedication to cultivating our service provision allows Lucy Electric to offer a complete solutions package to our customers; facilitating the delivery of electricity to homes and businesses worldwide.
Does this sound interesting? We would love to hear from you. Our application process in quick and easy. Apply today!
See more jobs in Vadodara, Gujarat